|
Compressed Air
Systems
For
industrial use or process air requirement , the air should be
clean and free from moisture.
When air is compressed to 7Kg/cm²g, the temperature of
discharged air increases to around 140°C. The after cooler and
separator installed after the compressor are to the remove the
moisture and oil. As an example, a 100Nm3/hr capacity
compressor with suction conditions of 40°C & 50%RH when
compressed to 7.0 kg/cm²g and subsequently cooled to 40°C will
result in condensation of around 30lits of water. The air
still will contain 8000ppm moisture. At 45°C, compressed air
contains 10,500ppm, at 50°C, 13,500ppm moisture and at 60°C,
21,600ppm moisture which are to be removed by Air Dryer.
Therefore, lower the temperature of air entering the dryer
inlet, smaller would be the size of Air Drying unit and batter
the performance.
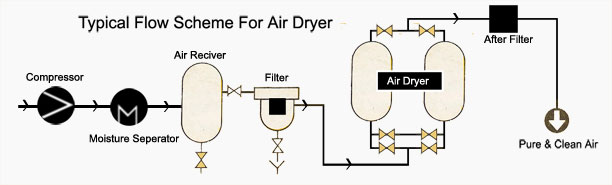
Salient Features
-
The cooling water supply is not
required.
-
Low temperature operation reduces
corrosion of towers and desiccant lasts longer.
-
Automatic repressurizing equalizes
desiccant chambers pressure before changeover, thus avoiding
any bed movement at the time of changeover.
-
High performance, low initial
installation and operating costs. Maintenance free and no
heaters to burn out.
-
Soft seated pneumatic Control
Valves are used for isolation of towers allowing no internal
or external leakage as noticed in 2/3 ways Plug Valves.
-
Only single phase electric power
is required for operating solenoid valves. Power consumption
is negligible.
|
|